From | Message |
Dan M Dodge Dakota JOIN HERE 
3/14/2006 06:46:55
|
Subject: metal work IP: Logged
Message: First I'm not a metal guy, I can't weld (wish I could!) and do not know much about working with metal.
I just installed front and t-case skid plates and am looking at more protection for offroading and road debris. I do alot of highway driving in darkness (I go to work at 5am) and have ran over more than my fair share of tire debris.
I have a 2002 QC 4x4 with 4.7L and am not too happy with the plastic piece that protects the underside of the engine bay by the bumper. This is the plastic piece with the little hole for changing the oil filter.
I am wanting to remove it and install some sort of metal piece instead. I've been looking online and can find some steel are good prices. I'm looking at diamond plate or plain steel sheets.
It looks easy enough to use a torch and heat up the metal and bend it in my vice. Has anyone done anything like this before? Pictures would be appreciated.
Can someone point me to a website to better educate myself about this kind of metal work?
Anyone have any other ideas to better protect the oil filter?
- Dan M
|
OBIO3 Dodge Dakota JOIN HERE
3/14/2006 22:47:23
| RE: metal work IP: Logged
Message: Forget the diamond plate. All those humps make it dificult to drill holes exactly where you want/need them. 3/16 is as thick as you want it. even that is getting on the heavy side. The torch is good for cutting provided your good at it. Otherwise, your going to be buying a lot of grinding wheels and spending a lot of time smothing the cuts. The really smart thing is a 4 inch hand grinder with the thin cut off wheels. Buy quality wheels only or you will be very disapointed in performance. Mark your plate on the opisite side you want to bend it. cut your way through 60 or 70 percent. This makes the metal really easy to bent and it will bend exactly as you want it. Now the part you don't want to hear. Get a wire feed welder. Mig that uses gas to shield the welding wire. Wire feed welding is not dificult at all. Make sure the plate is bent exactly as needed and set it on the ground with the cut side up. SPOT weld, That is up to 1/2 inch long welds every 4 or 5 inches. This is to keep the heat from worping your work. After spot welding all the way across, weld it solid. WALLA.... Suprise.... It will look good. Once you weld these plates, your going to have yopur brain working overtime figuring what you wil build next. A Miller 130 welder ythat runs on 110 is a very impressive welder. DO NOT BUY A CHEAP PIECE OF JUNK. You will regret it from day one. TIP.... The stinger cable should be for .035 wire but buy only .024 or .025 wire..... Which ever is available. The stinger tips need to be the proper size for the wire. again... .024 or .025 tips. Doing this WELL make your welder run a lot smother. Trust me here. I been doing this for over 30 years now.
|
Kowalski GenIII

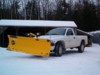
3/15/2006 18:30:08
| RE: metal work IP: Logged
Message: Good tips there - I just learned to mig weld a couple years ago. The machine's instructions will help you with the feed and power settings for a given thickness, but basically when you hear it sizzling and crackling your getting a good bite. Go too hot and you'll burn through the metal; you can fix that by going to a lower power setting and tickling the trigger instead of holding it full on to build the metal up again. To fix a larger burn hole, you might need to weld a washer or other metal back in. A little practice and you won't be burning holes anymore. You'll get a feel for how the wire feels when you're getting a good bite after a while - you can kind of feel it pushing into the work just a little, in addition to the sound. You'll feel it pushing harder with too fast a feed rate. They make some nice helmets now that go from clear to protected instantly, you'll want a decent one (I went with Miller), the cheap ones darken slower and have a cloudy view.
Lead, follow, or get out of the way
|
Terry Dodge Dakota JOIN HERE
3/15/2006 20:11:41
| RE: metal work IP: Logged
Message: Excellent info from OBlO3 and Kowalski. They're right - you don't need 220V to run a nice little MIG welder. Only one other thing: Collect a few scraps of metal and practice welding them together in different ways before you start fabricating. Like Kowalski said, get the feel for it first. Most welders come with some kind of instruction video, and if not, you can easily get one from a supply shop or even the library. But you probably won't need it. You'll be surprised at how easy it is, and it'll make the final result that much more rewarding. "Weld for a man, and you've helped him with that job. Teach a man to weld, and he'll do his own jobs for the rest of his life." Have fun.
|
OBIO3 Dodge Dakota JOIN HERE
3/15/2006 20:49:09
| RE: metal work IP: Logged
Message: I should have mentioned. Pay attention to the duty cycle of the welder. I have always pushed mine a little beyond recomended time and got to tell you, my welder has really impressed me time and time again. However 10 or12 years down the road I managed to burn out one diode(there are 2 in mine). I rep;aced both at that time. Been several years go and all I recall is 40 bucks. not remembering if that was for 2 or each. Here's the deal. As you push the welder beyond recomended duty cycles, you burn holes in the diodes(internally).When you get enough holes in them,they weaken and WALLA, one will give out on you. No big deal. Just information so you don't go off the deep end should your welder ever give up the ship on you.
So many problems .... So little time
|
bigdave Dodge Dakota JOIN HERE
3/16/2006 09:06:55
| RE: metal work IP: Logged
Message: The Sears brand welders are pretty good. I have been using mine for over 3 years for about 5 to 6 hours a week. I personally prefer .030 wire with 75/25 gas. I also use it for welding aluminum which works relatively well without a spool gun. Once you get a welder, it will be your favorite tool, you will wonder how you lived without one before.
|
| P 1 |
|
Post a reply to this message:
Username Registration: Optional All visitors are allowed to post messages
|